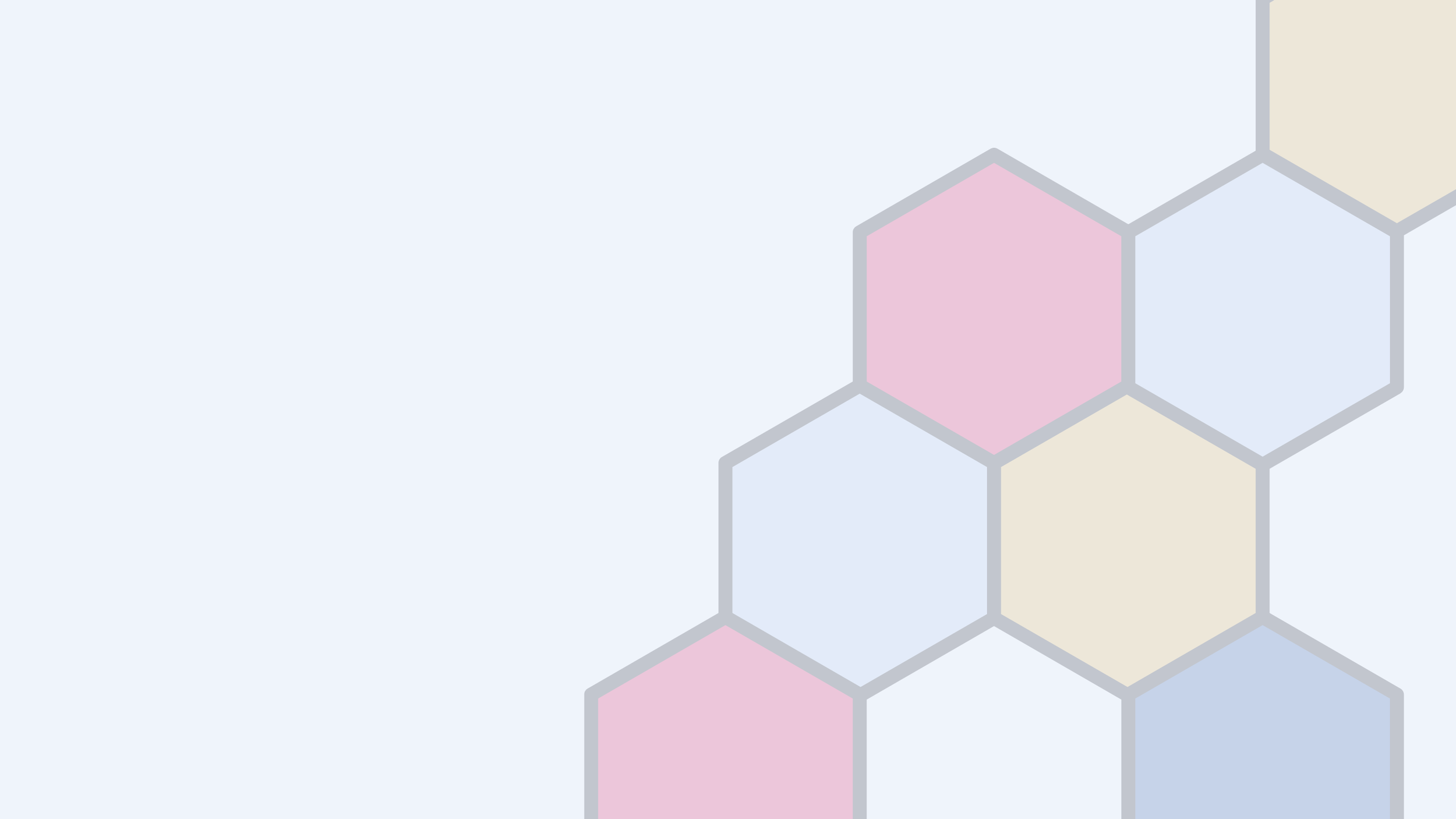
Support Videos
Explore our self-guided support videos.
Agnostic Kits
Use Freezerworks Pinnacle's Agnostic Kits to make your study management more flexible and efficient.
What can Freezerworks do for you?
Freezerworks is a fully-configurable solution for sample tracking, sample management and freezer inventory.
The Freezerworks Hierarchy
This video will walk you through the hierarchy of Freezerworks. Learn how you can use Transactions, Aliquots, Samples, Patients, Visits, and Studies to better manage your data.
What’s New in Freezerworks 2024
Freezerworks 2024 is here! Here's what you need to know about the new features and functions in this powerful new edition.
Workflows on the Browser Client: Part 2
Learn how to use additional workflow types on the Freezerworks Browser Client.
Pooling Part 2 (Browser): Search and View
Using Pooling-related fields and a new type of search, learn how to effectively find your Pooled Samples in the Freezerworks Browser Client.
Pooling Part 1: Workflows
Using Pooling-related fields and a new type of search, learn how to effectively find your Pooled Samples in the Freezerworks Desktop Client. This video also details how our new traceability tools and Pooling tabs in Samples Entry make it easy to discover everything related to a Pooled Sample
Pooling Part 2 (Desktop): Search and View
Using Pooling-related fields and a new type of search, learn how to effectively find your Pooled Samples in the Freezerworks Desktop Client.
What’s New in Freezerworks 2022
Freezerworks 2022 is here! Here's what you need to know about the new features and functions in this powerful new edition.
Workflows on the Browser Client: Part 1
Learn how to use additional workflow types on the Freezerworks Browser Client.
Patient Management for the Browser Client
Watch as we demonstrate how to create and modify Patient data with the Freezerworks Web Client. Learn how to configure Patients Entry Forms, add new Patients, associate Samples to Patients, and more.
Samples Entry: Part 2
Watch as we demonstrate how to create and modify Sample Entry Forms for the Browser Client. Learn how to add fields, color, branding, and more to your Entry Forms.
Samples Entry: Part 1
Watch as we demonstrate how to enter Samples and Aliquots on the Web Client. Learn how to use the Entry Forms to add and modify data.
What's New in Freezerworks 2021
Upgrade your lab operations with Freezerworks 2021! Discover the Web Client features that make sample management smarter and faster.
Reports: Part 2
In this video, you'll learn how to print reports from the Inventory List View, Sample Records, Explore Freezers, or Shipments.
Reports: Part 1
In this video, you'll learn how to print reports from the Inventory List View, Sample Records, Explore Freezers, or Shipments.
Sub-Aliquot Workflows: Part 2
Now that you know how to configure a Sub-Aliquot Workflow, let's learn how to process it.
Sub-Aliquot Workflows: Part 1
Learn how to configure a Sub-Aliquot Workflow Template in Freezerworks 2019.
Visual Freezers: Part 4
In this final video on Visual Freezers, we'll show you how to set up a freezer's subdivisions before configuring its picture, then finish with an example of an exception.